Inscrivez-vous à notre bulletin d'information
pour rester au courant des dernières tendances et nouveaux designs HFLOR/HIMACS.
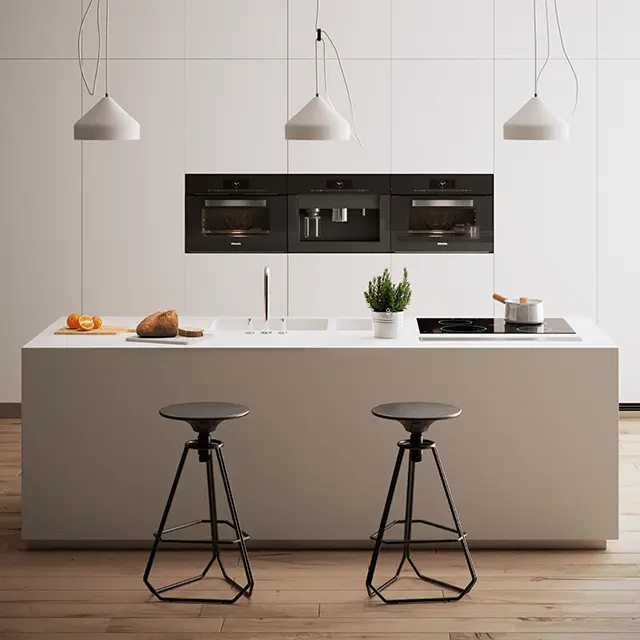
HIMACS: Table SLO_GEN
La table Organique SLO_GEN conçue en HI-MACS® étonne les visiteurs dans les bureaux Gensler
La table commune SLO_Gen est résolument le nouveau point fort du hall d’entrée des bureaux Gensler à Los Angeles. Elle est le résultat d’un partenariat innovant entre Gensler et le Departement d’Architecture du College of Architecture and Environmental Design, à l’Université Cal Poly de San Luis Obispo (Californie).
Ses courbes sinueuses toutes en finesse ont été réalisées grâce à HIMACS, un matériau unique de par ses propriétés de thermoformage, de résistance, et d’assemblage sans joints apparents. Sa surface lisse a su convaincre les architectes et les ingénieurs au premier coup d’oeil.
En 2011, les professeurs Jim Doerfler et Mark Cabrinha, co-directeurs du Digital Fabrication Lab (« d[Fab]Lab ») de Cal Poly, ont fait appel à Shawn Gehle, responsable du design chez Gensler L.A., pour créer un studio entièrement virtualisé, centré sur la fabrication numérique et les outils de collaboration en ligne.
Pour répondre à cette demande, Shawn Gehle a élaboré un séminaire sur 10 semaines qui permettrait aux étudiants de bénéficier de l’expertise de la société en matière de design et d’explorer les techniques de fabrication numérique et de recherche de formes à travers la conception d’un meuble sur mesure.
Le cahier des charges évoquait simplement un meuble autour duquel les invités pourraient se tenir debout ou assis, et un espace de rangement dédié aux publications de la société sur le design. Le meuble devrait être spécifique au site et serait intégré dans le nouveau prestigieux bureau de Gensler en plein centre de Los Angeles.
Un prototype virtuel en 3D
Suite à une première rencontre, les étudiants de Cal Poly et la faculté d[Fab]Lab ont fait la connaissance de conseillers de chez Gensler par le biais d’un outil de collaboration en ligne, GoToMeeting, grâce auquel ils ont pu mener des discussions hebdomadaires et analyser la progression de l’équipe. En plus de combler le fossé de 500 km séparant les designers de Los Angeles des étudiants ainsi que des professeurs de la faculté à San Luis Obispo, cette méthode a permis à des consultants professionnels et spécialistes des matériaux de participer plus aisèment à ce projet. Procéder de cette manière a notamment permis aux étudiants, d’avoir accès à la collaboration virtuelle, pratique indispensable dans les méthodes de travail de notre génération. Privilégiant un flux de travail numérique, le processus de documentation et de conception de l’équipe a également été mené virtuellement, substituant comme livrable un modèle en 3D au traditionnel dossier de dessins en 2D.
Au cours du séminaire, les concepts originaux de trois étudiants ont été développés et affinés à l’aide du logiciel de modélisation Rhinoceros 3D avec T-Splines, et virtuellement analysés et améliorés chaque semaine par le personnel de Gensler.
Les ingénieurs en structure de Buro Happold et le fournisseur de la pierre acrylique HIMACS LX Hausys se sont joints à de nombreuses discussions pour examiner les plans et donner leur avis sur la faisabilité, le coût et l’intégrité structurale. Une dernière rencontre en personne à Los Angeles s’est attelée à analyser les prototypes physiques et échantillons de matériau, et a permis à l’équipe d’aborder les défis que représentait la fibre de verre par rapport au Solid Surface HIMACS pour constituer le matériau de surface prédominant de la table.
Inspiré par le design et le défi, LX Hausys est devenu un partenaire du rpojet, fournissant une expertise et uneaide technique qui s’est avéré le matériau idéal pour réaliser la surface drapée de la table. LX Hausys a également mis l’équipe en relation avec R.D. Wing Co. Inc., des spécialistes de la fabrication basés à Seattle qui ont finalement construit et livré le design de la table.
La table SLO_Gen a été récemment installée dans le hall d’entrée principal de Gensler Los Angeles, où sa silhouette théâtrale continue d’attirer les passants à l’intérieur et de susciter des questions sur son origine. Grâce à l’exceptionnel rendu de HIMACS en association avec d’autres matériaux, la couleur blanche du Solid Surface crée un contraste doux et élégant avec le bois naturel.
Intégrer le contreplaqué au Solid Surface HIMACS
Des coupes pour les côtés en contreplaqué de la table ont été extraits du modèle en 3D et posés sur des feuilles de 1,2 x 2,4 m d’Europly pour l’usinage CNC. La table nécessitait 12 feuilles de contreplaqué pour réaliser la structure en entier. Pendant le processus de fabrication, des ont été laissées le long des bords pour faciliter l’assemblage et parfaire les finitions. Les languettes ont été taillées, limées et sablées à la main. Cette méthode de fabrication permettait de sauvegarder les formes prédéfinies pendant l’usinage, afin d’éviter qu’elles ne cassent et de ne pas endommager les surfaces visibles de la table par de l’adhésif ou des vis. Après avoir coupé les languettes, les jointures ont été vernies pour une finition satinée. Une fois le vernis sec, la structure en grille a été assemblée à la main à l’aide d’un maillet et de lambris d’appui.
Thermoformage et intégration de HIMACS avec le bois
Pour commencer avec le plateau en forme de S, 4 pièces distinctes de HIMACS ont été fraisées sur un routeur CNC. Ce nombre était dû à la taille limite du matériau en stock et aux dimensions globales de la table. Les pièces produites ont ensuite été collées ensemble et sablées, représentant un seul plateau en pierre acrylique. Une bande d’1,5m de large (en plusieurs morceaux) a été produite pour suivre la courbe du plateau. Cette bande a été utilisée comme une courroie de secours là où le flanc de la table rencontre la face cachée du plateau. Cette courroie a été collée sur place, avec des ondulations réalisées dans son profil pour aider l’atelier à aligner les flancs plus tard dans le processus.
Etant donné le degré de courbure des panneaux latéraux de la table en HIMACS, la définition des morceaux et l’assemblage de la surface constituaient une étape délicate. Il s’agissait de déterminer quelles portions du Solid Surface pouvaient être usinées en forme sans moulage lesquelles exigeaient des moules et de quel type, et où et comment définir au mieux les morceaux de l’ossature de la table pour optimiser le matériau fourni par LX Hausys.
Pour optimiser le matériau, augmenter la performance du Solid Surface et harmoniser les nuances, chaque flanc de la table a été divisé en 5 sections à partir de la topographie de la surface globale. R.D. Wing a créé un ensemble de moules (aucun moule n’était identique) pour fabriquer chaque flanc. Le seul moyen de réussir les parties les plus compliquées du flanc avec la pierre acrylique était d’utiliser un moule à clapet, permettant au matériau d’être thermoformé par pression simultanée appliquée à l’avant et à l’arrière. Cette technique demandait de fraiser deux moules pour chaque section formée, un mâle et un femelle. Il a fallu prêter une attention supplémentaire à la taille des moules (et par conséquent, à la quantité de matériau nécessaire).
Pour créer les moules de thermoformage, R.D. Wing a utilisé entre 6 et 9 kilos de mousse polyuréthane, des restes non utilisés d’anciens projets. Les côtés des moules ont été laissés inachevés, ainsi les moules de chaque section ont pu être réutilisés jusqu’à 10 fois si nécessaire. La mousse a été montée sur une base de MDF et fraisée avec un routeur CNC en piles de 1,27 cm. Chaque couche a été usinée, puis une nouvelle couche de matériau a été ajoutée par-dessus. Ce processus a été répété jusqu’à ce qu’un moule entier soit réalisé. Une étape de fabrication a été additionnée afin d’éliminer le besoin de ponçage. Une ligne de découpe a été ajoutée autour du périmètre des moules afin que l’atelier puisse voir comment un panneau s’emboîtait dans un autre. Lorsque tous les moules ont été fabriquées et nettoyés de l’excédent de mousse, une couche de coton a été appliquée en surface pour la dispersion de la chaleur.
Pour les plus grandes portions de HIMACS demandant un thermoformage dans deux directions (courbes complexes), les morceaux ont d’abord été chauffés, puis placés dans le moule à clapet. Sur les 5 moules, il a fallu 12 morceaux de HIMACS pour faire tous les côtés. Après plusieurs essais et erreurs, le nombre de morceaux nécessaires a pu être défini. Après avoir grossièrement formé les 12 morceaux, ils les ont replacés dans le moule et ont commencé à les agencer pour la dernière découpe. Chaque pièce a été réalisée en fonction de la taille correspondante et ensuite collée ensemble. Les plus petits morceaux ont été assemblés pour former 5 pièces principales.
Les morceaux latéraux ont été pré-collés en 5 pièces utilisables, puis ajustés sur les flancs de la structure en bois. Les pièces latérales ont été adaptées à la face cachée de la table contre la courroie d’assemblage incluse dans le plateau, maintenant les côtés fermement contre la structure en bois, et rassemblant le tout pour l’assemblage.
L’étape suivante consistait à découper le fond rainuré et le côté qui faisaient face aux étagères, puis à couper droit le côté assemblé et créer un bord plat pour l’unir à la face cachée de la table. Après avoir collé la première section à la face cachée de la table et siliconé l’arrière de la première section à la structure en bois, la section suivante a été pré-adaptée au dessous de la table et à la section correspondante. Cette approche demandait de couper la forme en laissant le moins d’intervalle possible, puis de la limer à la main pour l’installation finale. Une fois bien en place, le processus a été répété autour du périmètre.
Une fois toutes les sections assemblées, toutes les surfaces exposées ont été sablées. Il ne restait plus qu’à terminer le ponçage de toute la surface et à éliminer les petites imperfections.
Une fois fabriquée, toute la table a été montée à l’intérieur d’une caisse conçue spécialement pour l’expédition et la livraison.
Emplacement | Gensler Los Angeles, Los Angeles (Californie, USA) |
Architecture & Design | Cal Poly, San Luis Obispo, Department of Architecture, College of Architecture and Environmental Design Faculty: Jim Doerfler, Mark Cabrinha Students: Ben Hait-Campbell, Cory Walker, Kegan Charles Flanderka Gensler LA |
Fabrication | R.D. Wing Co., Inc. |
Crédit photo | ©Gensler Los Angeles |
Communiqué de presse Télécharger le communiqué de presse |
Project gallery
-
Télécharger les images
Si vous êtes journaliste, il est possible de sélectionner les médias que vous souhaitez et de nous demander de vous les fournir en HD.
DEMANDER CETTE IMAGE EN HD -
Télécharger les images
Si vous êtes journaliste, il est possible de sélectionner les médias que vous souhaitez et de nous demander de vous les fournir en HD.
DEMANDER CETTE IMAGE EN HD -
Télécharger les images
Si vous êtes journaliste, il est possible de sélectionner les médias que vous souhaitez et de nous demander de vous les fournir en HD.
DEMANDER CETTE IMAGE EN HD -
Télécharger les images
Si vous êtes journaliste, il est possible de sélectionner les médias que vous souhaitez et de nous demander de vous les fournir en HD.
DEMANDER CETTE IMAGE EN HD -
Télécharger les images
Si vous êtes journaliste, il est possible de sélectionner les médias que vous souhaitez et de nous demander de vous les fournir en HD.
DEMANDER CETTE IMAGE EN HD -
Télécharger les images
Si vous êtes journaliste, il est possible de sélectionner les médias que vous souhaitez et de nous demander de vous les fournir en HD.
DEMANDER CETTE IMAGE EN HD -
Télécharger les images
Si vous êtes journaliste, il est possible de sélectionner les médias que vous souhaitez et de nous demander de vous les fournir en HD.
DEMANDER CETTE IMAGE EN HD -
Télécharger les images
Si vous êtes journaliste, il est possible de sélectionner les médias que vous souhaitez et de nous demander de vous les fournir en HD.
DEMANDER CETTE IMAGE EN HD -
Télécharger les images
Si vous êtes journaliste, il est possible de sélectionner les médias que vous souhaitez et de nous demander de vous les fournir en HD.
DEMANDER CETTE IMAGE EN HD -
Télécharger les images
Si vous êtes journaliste, il est possible de sélectionner les médias que vous souhaitez et de nous demander de vous les fournir en HD.
DEMANDER CETTE IMAGE EN HD -
Télécharger les images
Si vous êtes journaliste, il est possible de sélectionner les médias que vous souhaitez et de nous demander de vous les fournir en HD.
DEMANDER CETTE IMAGE EN HD
Banque d’images

Ajouté à votre bibliothèque d'images
Allez à la page Banque d'images pour demander des images HD, ou cliquez sur OK pour poursuivre votre sélection.
Contact Presse
Mariana Fredes +41 (0) 79 693 46 99 mfredes@lxhausys.com
Agnieszka Papież +48 (0) 504 976 688 apapiez@lxhausys.com